Molded Rubber Formulations
Many of today’s engines use molded rubber gasket designs to provide extended service life and enhanced overall sealing.
Jim Daigle, Global Sealing Product Manager at Fel-Pro® Gaskets, points out that molded rubber is not “new” to engine sealing:
“Molded rubber gaskets have been in engines really as far back as the 1960s and 1970s, although they weren’t prolifically used. An early use was for what we call an oil pan end seal on the front and back of the oil pan. Typically, that application would use a molded rubber piece to seal the hoop. It was in the 1980s that OEMs started to employ molded rubber more across the engine, specifically for valve cover gaskets and oil pan gaskets. In the 1990s we started seeing the OEMs using molded rubber for intake manifold gaskets. Molded rubber is pretty common now on most modern engines. However, the types of rubber, the rubber formulations and the expectations for sealing an engine are very different from what they used to be. In addition, we are now leveraging new design elements, advanced molding capabilities and the ability to apply rubber to carriers.”
Although the rubber compound of some gaskets may appear similar – even attempting to mimic the look of Fel-Pro® products – the similarities end when the gaskets are put to the test in the repair environment. (Visually comparing two gaskets won’t show the differences between the molded rubber properties and formulations.) Fel-Pro’s proprietary in-house molded rubber technologies are unrivaled in the industry. All materials are tested and validated to ensure every gasket is manufactured using the best material for that specific application. Two of the most common molded rubber types used in Fel-Pro gaskets are silicone rubber, and fluoroelastomer (FKM).
When asked about the differences between molded rubbers among manufacturers, Steve Kueltzo, Global Engineering Director for Fel-Pro Sealing and Engine Parts, lays it out:
“At Fel-Pro, when our engineering team looks at a new application, we dive deep into the application and the environment being sealed, understanding the sealing stresses put on the gaskets. Then we will work with our chemists to select the specific molded rubber formulation for that application and add the design features needed to create a robust seal. We do a lot of behind-the-scenes testing to make sure it’s right for the application, and before any gasket is manufactured or introduced into the repair market, it’s approved through our validation process. Regardless of the material or the gasket, we validate every part we sell.”
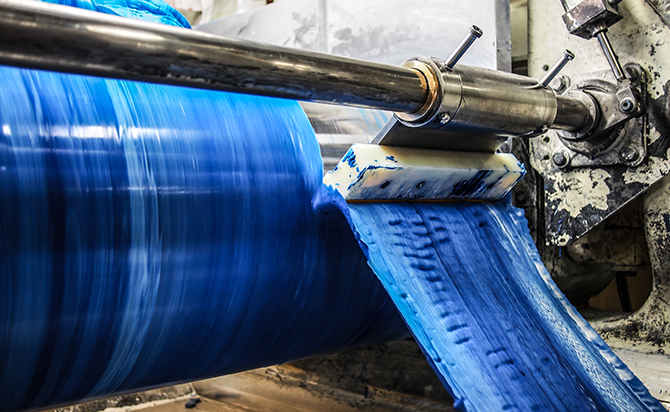
Silicone
There are many different types of silicone rubber. At Fel-Pro, we maintain control over the exact blend of compounds used to create the rubber, testing each batch. This quality control continues through the manufacturing process, ensuring the mix is perfect. In-house manufacturing also allows us to make different blends of rubber for different applications, to suit specific needs.
The basic advantages of Fel-Pro’s silicone rubber are its long life, high temperature and oil resistance, and its ability to be used as a flexible press-in-place gasket or molded over a rigid carrier for easy installation and high vacuum holding capabilities. Silicone’s ability to resist extreme temperatures and maintain sealing pressure over time makes it ideal for sealing a wide variety of oil applications, such as valve cover and oil pan gaskets.
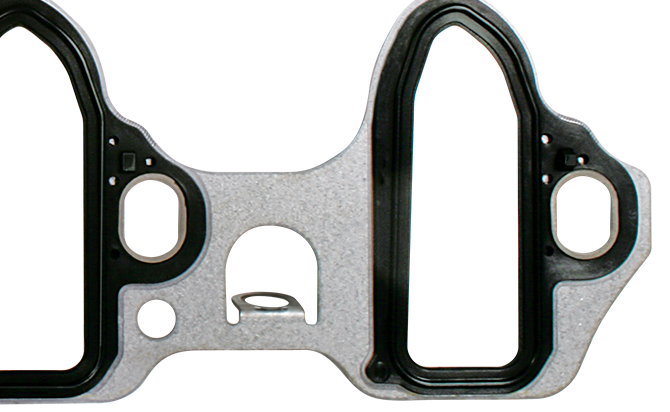
Fluoroelastomer/FKM
FKM, also known as fluoroelastomer, is a synthetic rubber compound that has resistance to a wide variety of chemical compounds. At Fel-Pro we use our proprietary FKM formulation, which is designed specifically to hold up to the chemicals found in modern engine fluids.
FKM can be used for molded rubber gaskets and as a gasket coating. Fel-Pro engineers use a blend of ingredients to make a proprietary FKM rubber that is impervious to all types of oils and fluids. This premium rubber is molded to a rigid carrier system, like the Fel-Pro PermaDryPlus® intake manifold gasket offering. Its proprietary properties make it ideal for intake manifold gasket sealing, where exposure to the corrosive properties of some coolants can cause premature gasket failure. FKM is also ideal for use as a head gasket coating, since it is conformable enough to seal minor surface imperfections, while being dense enough to retain torque and at the same time resist high engine operating temperatures
Fel-Pro PermaDry® molded rubber gaskets are designed as a replacement for applications that were originally equipped with molded rubber gaskets. The premium Fel-Pro PermaDryPlus® gaskets are problem-solving gaskets made for applications that are known to leak or are difficult to install. Whenever a PermaDryPlus gasket is available for an application, it is absolutely the best sealing option available. And like all Fel-Pro molded rubber gaskets, PermaDry and PermaDryPlus gaskets need to be installed without the use of any chemicals – CLEAN and DRY.